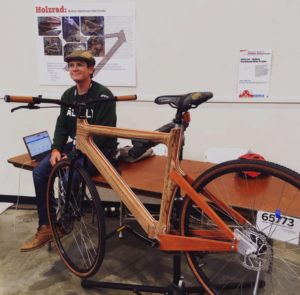
This post is about the first wood bike I made, and for that matter, the first bike I ever made. During my winter quarter at Cal Poly in 2018 I took a bicycle design class call Single Track Vehicle Design (henceforth referred to as ‘Single Track’). The main deliverable for the lab portion of this class was a functional prototype (read: rideable bike) based on Handling characteristics we decided individually.
I don’t know a whole lot about welding, and while I’d like to learn, the challenge of making a wood bike was too intriguing to me to pass up.
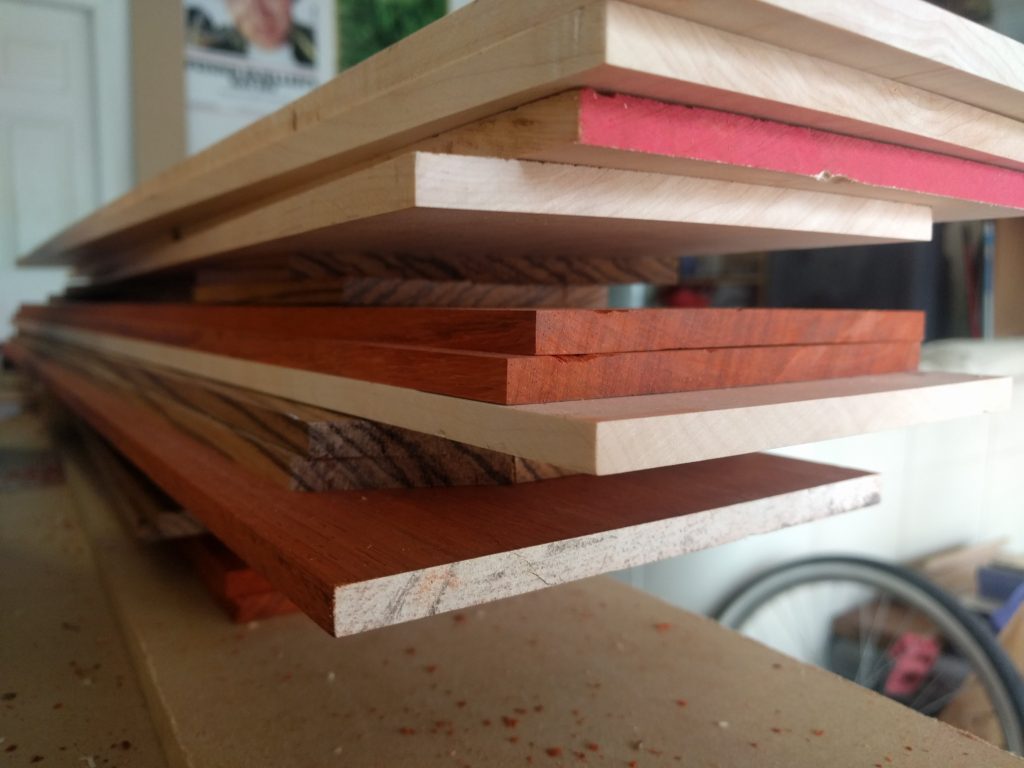
The construction of the first wood bike was trial by fire, taking place over the course of 5 weeks during the second half of the quarter in which I took Single Track. I’d never built a bike before, and I’d certainly never built anything out of wood this complex.
I did a lot of research into how one goes about the making of a wood bike. Some information existed at the time: a video or two from Renovo showing their manufacturing process, a fantastic guide by Nick Cole at Ligneus Bikes, a post by epoxy works, and a few others. I’ve found more and more sources in the year since I built this bike. Some of this is that there seems to be more people actually doing this, and some seems to be that I’ve searched in more places, one of the most prominent being Instagram interestingly enough.
The front triangle of the bike was made from 7 layers, each 0.3″ thick. The layers were each composed of four pieces, one for each of the tubes that comprise the bike’s front triangle: top tube, down tube, seat tube, and head tube. At the intersection of each tube, the layers were cut with a half lap joint. This provides lots of surface area for glue and forms a pseudo finger joint in the final glue up.
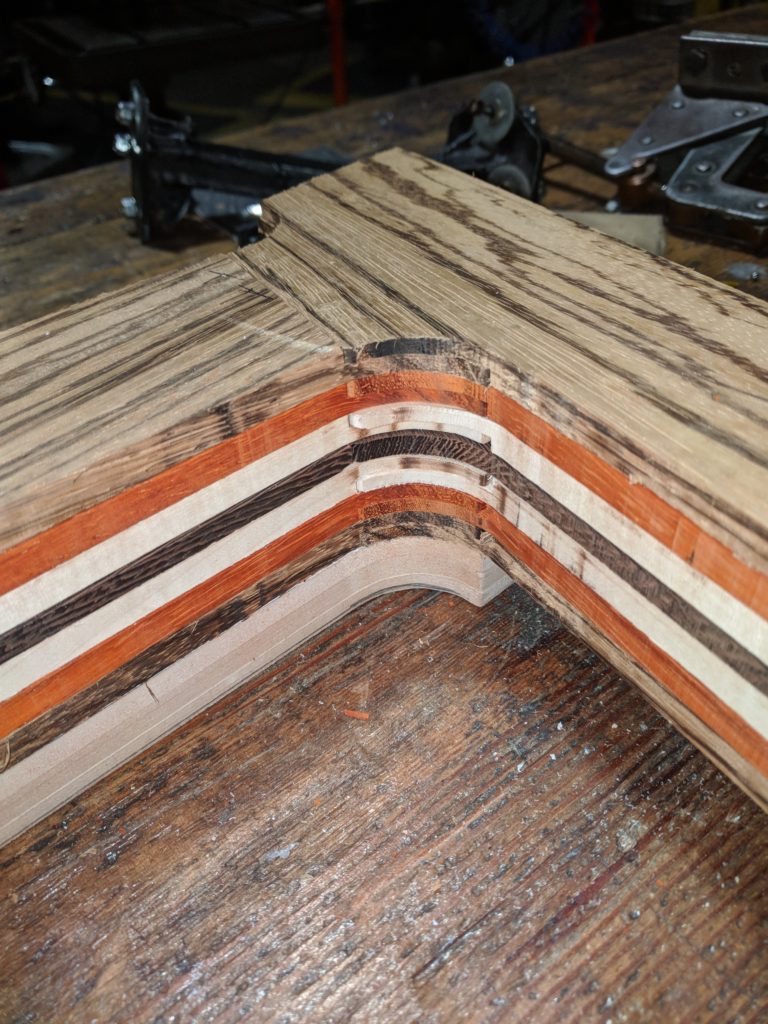
Wood is what is called an orthotropic material in the engineering world. This means that it’s mechanical properties are not the same in every direction. Every woodworker knows this intrinsically. The wood will be strongest along the direction of the grain. With this in mind, I wanted the grain to run along each of the four main tubes of the front triangle (yes I know that a triangle only has three sides, but in bike speak sometimes they have four).
So, I glued the main triangle in two parts so that I could remove most of the material in the middle of the frame to reduce weight. I used a mill in the school’s machine shop to remove the waste in both halves of the frame, cutting about 90% of the weight.
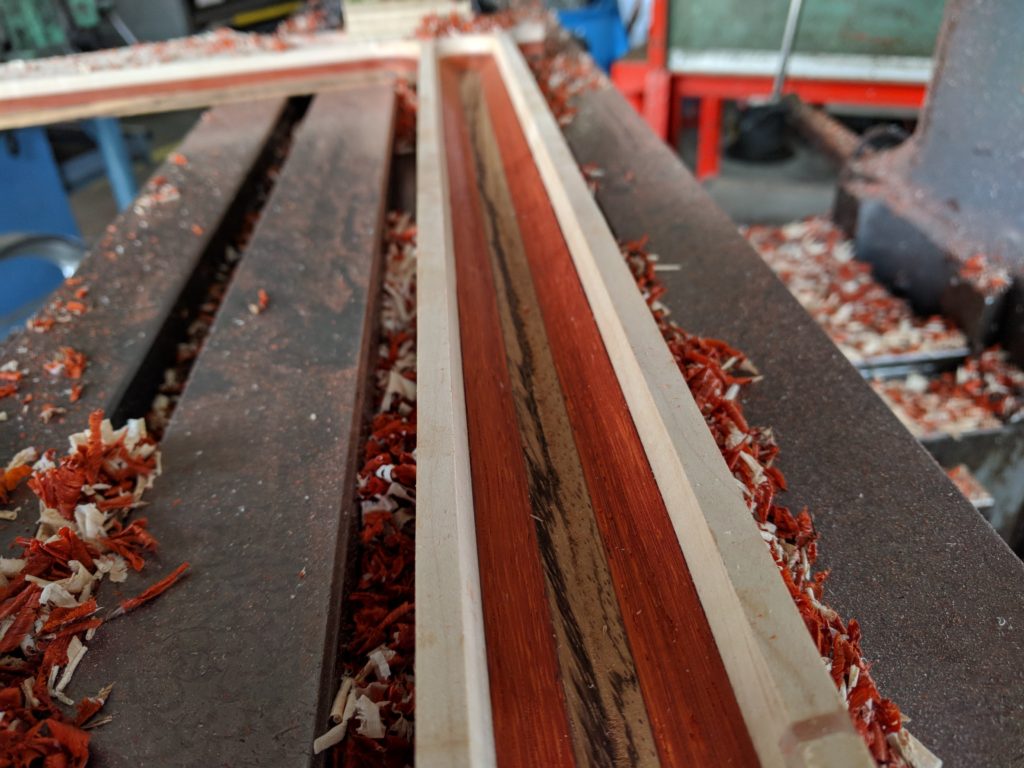